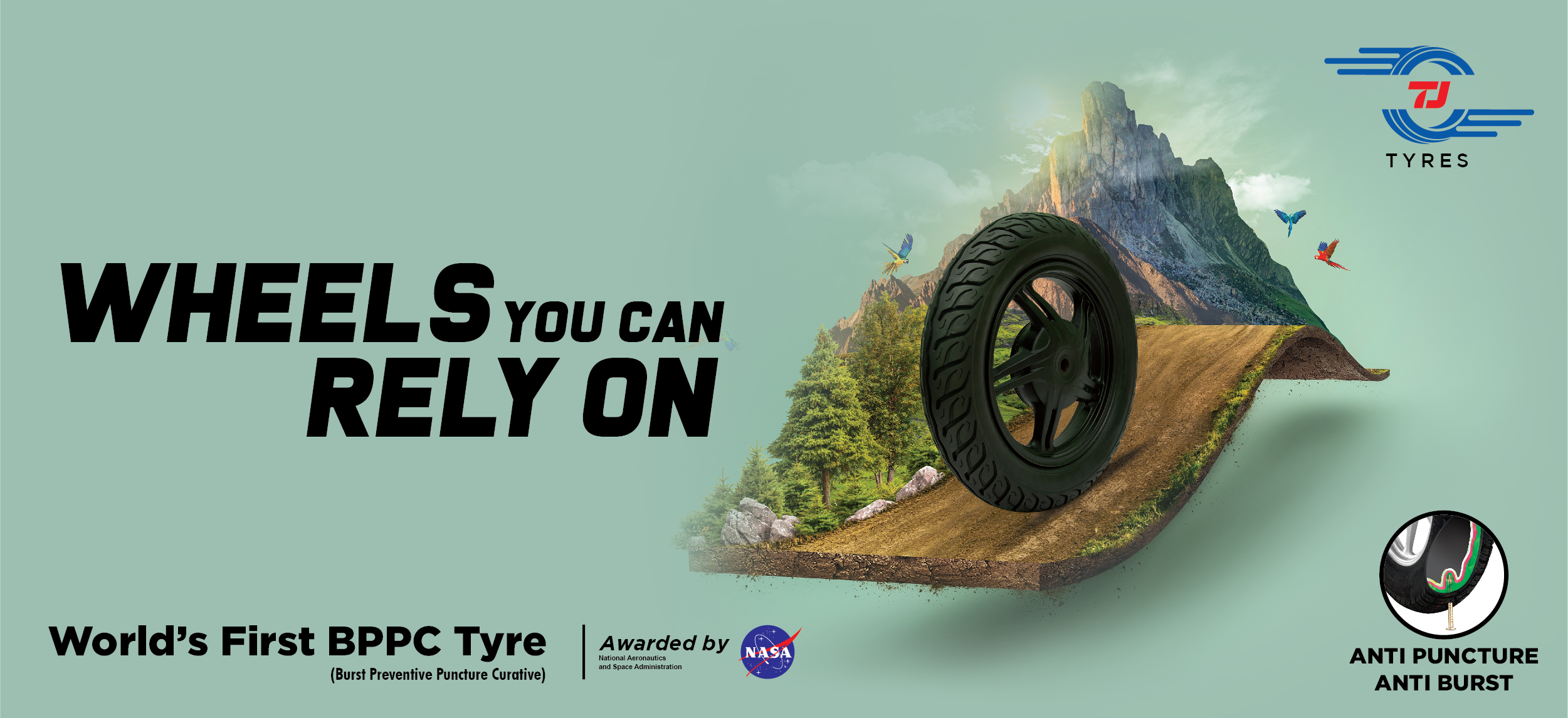
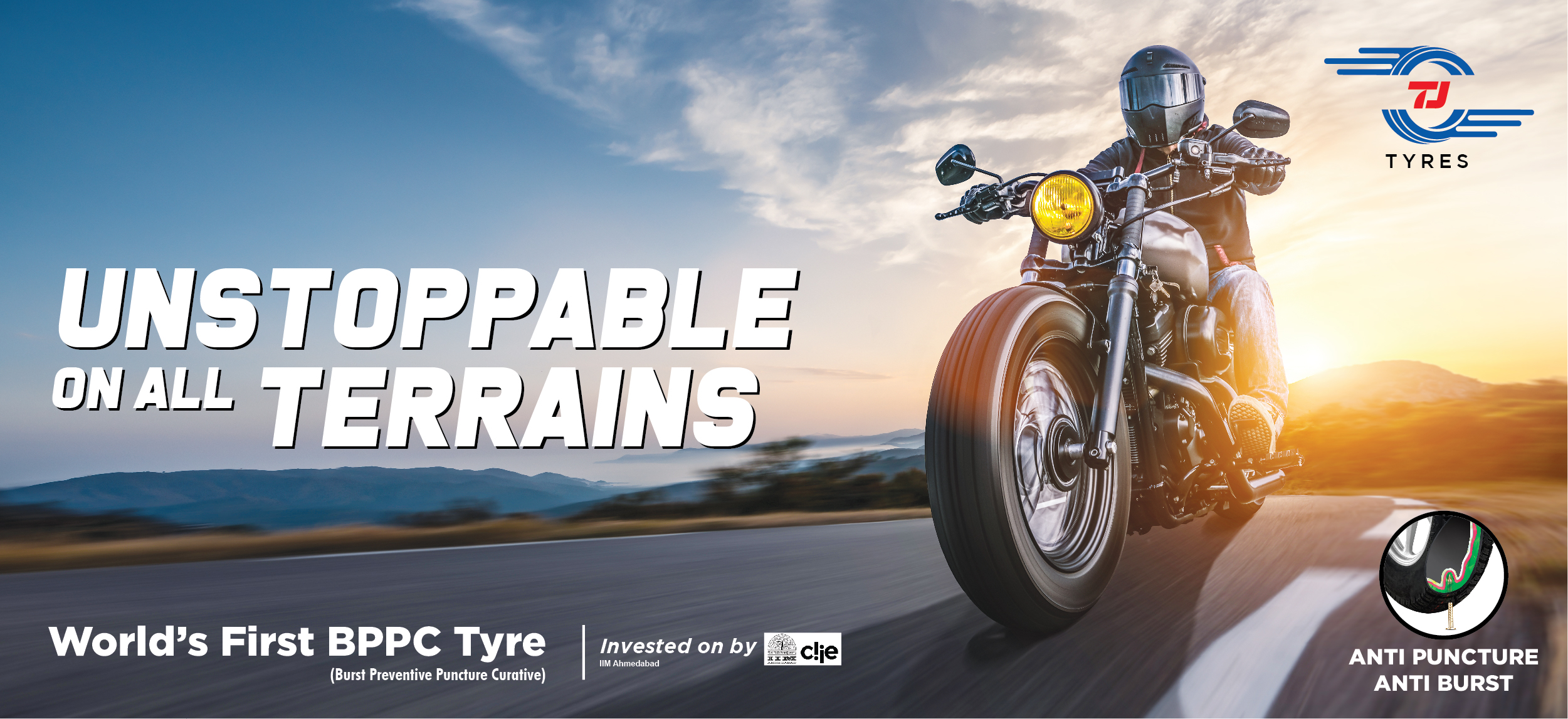
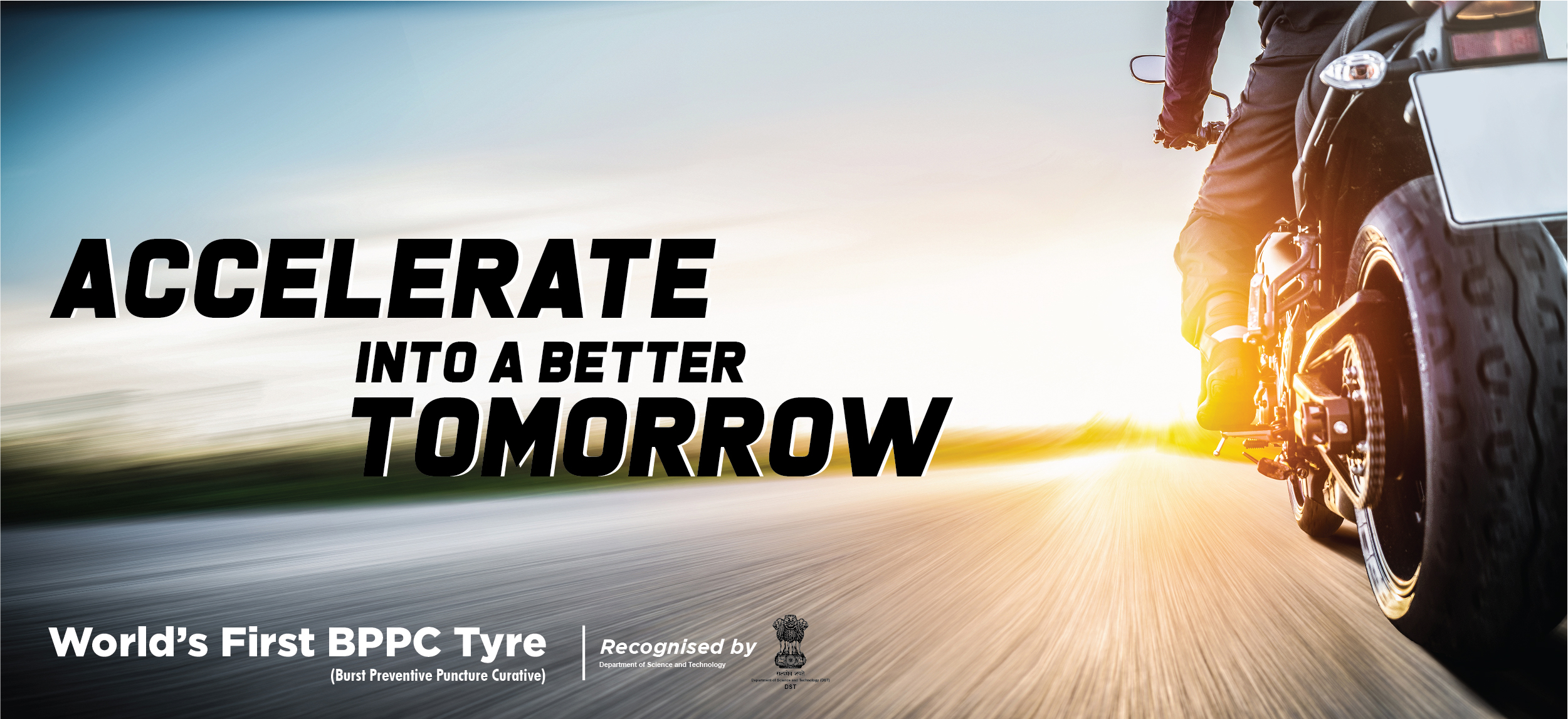
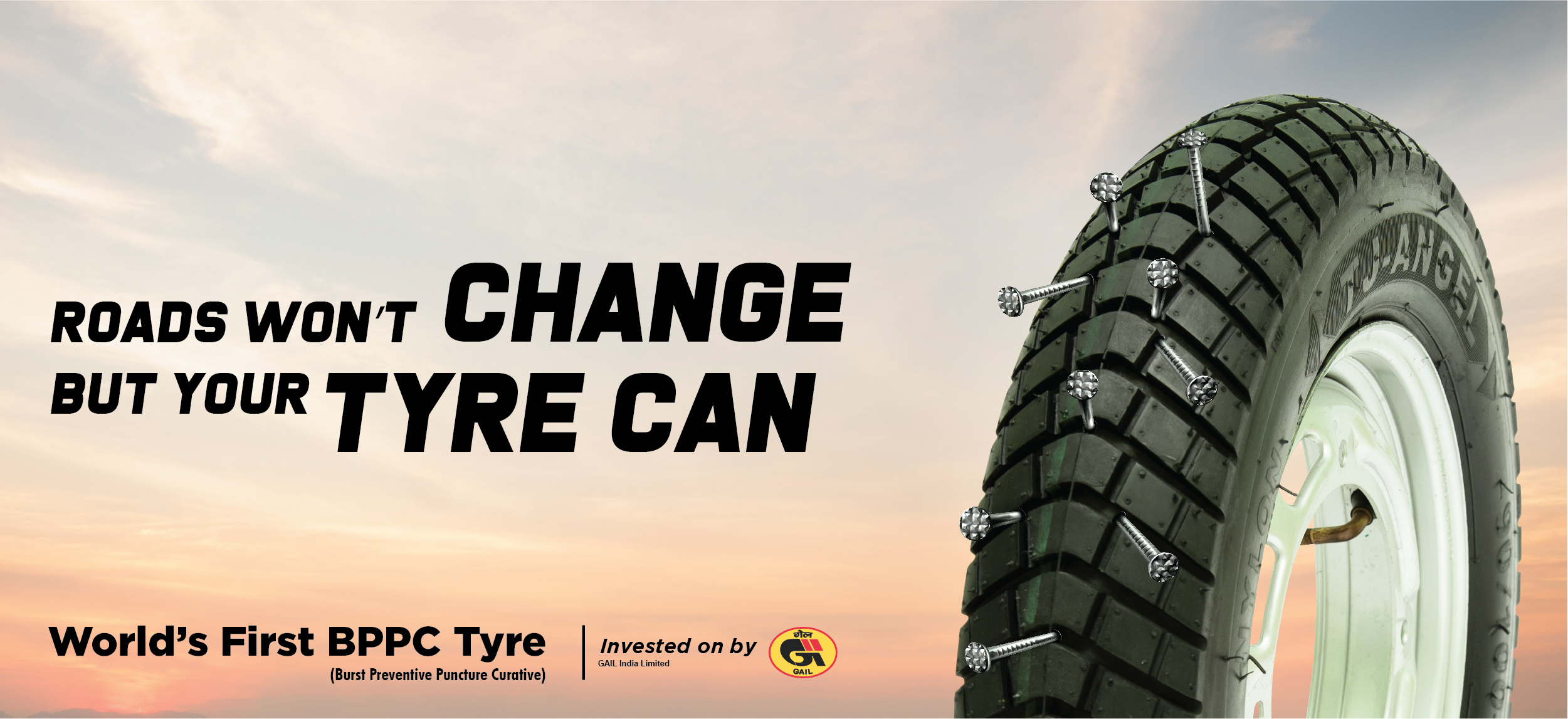
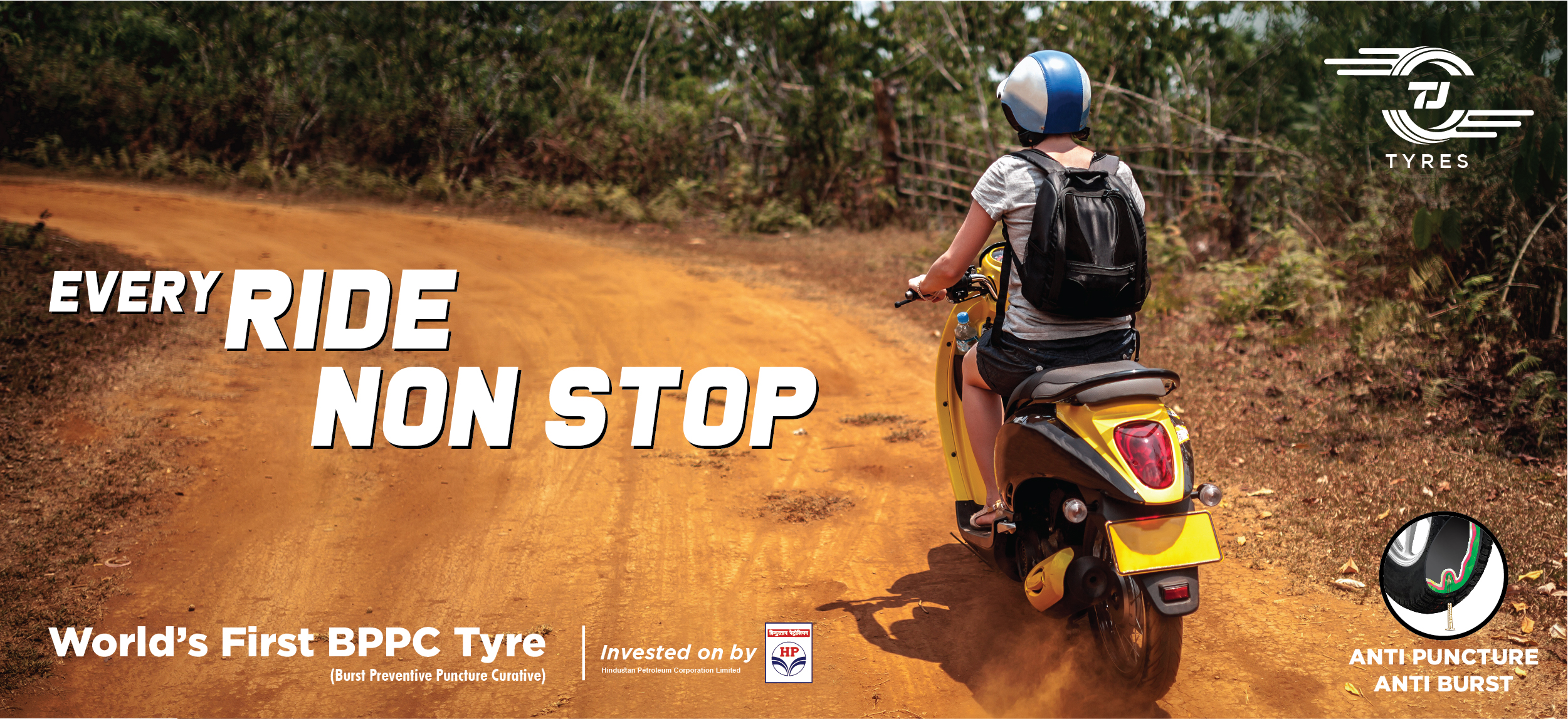
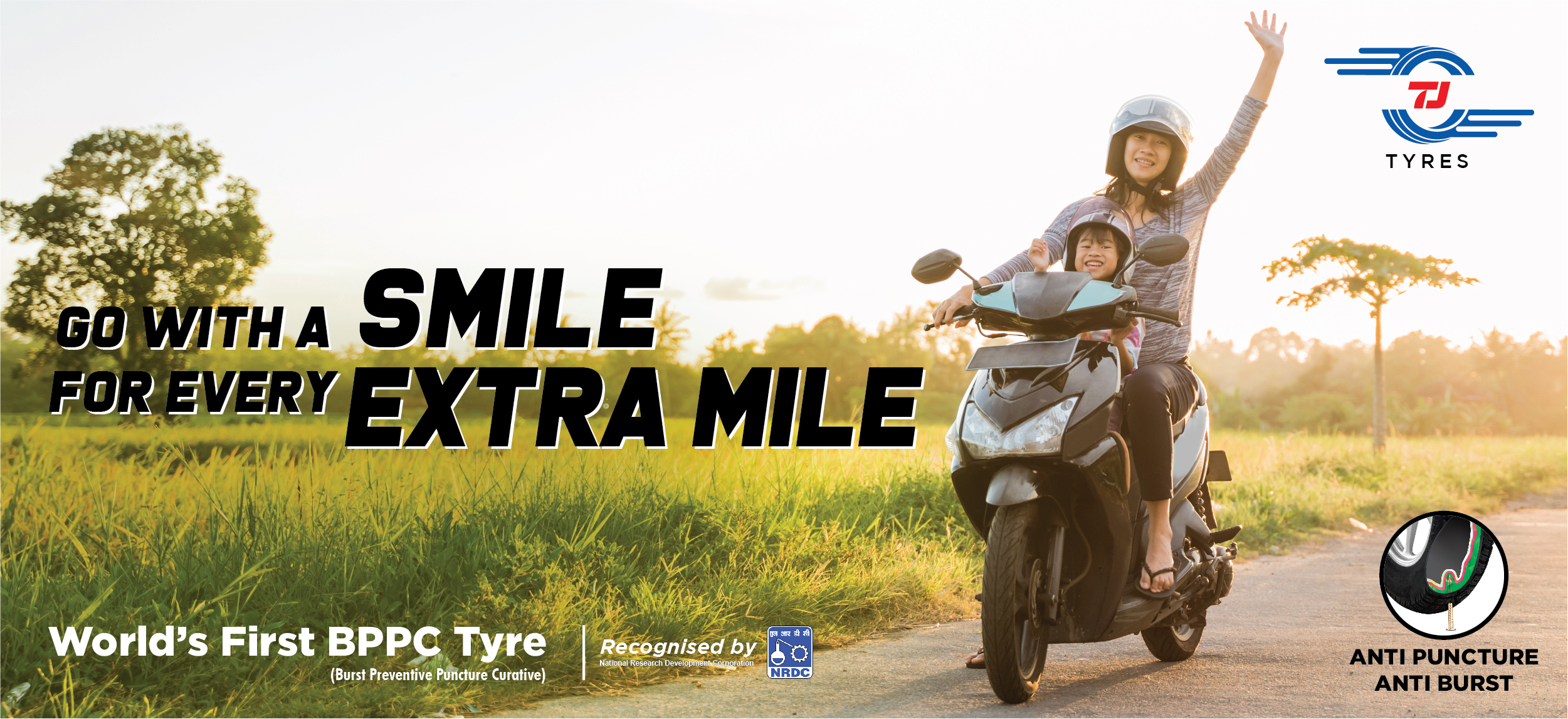
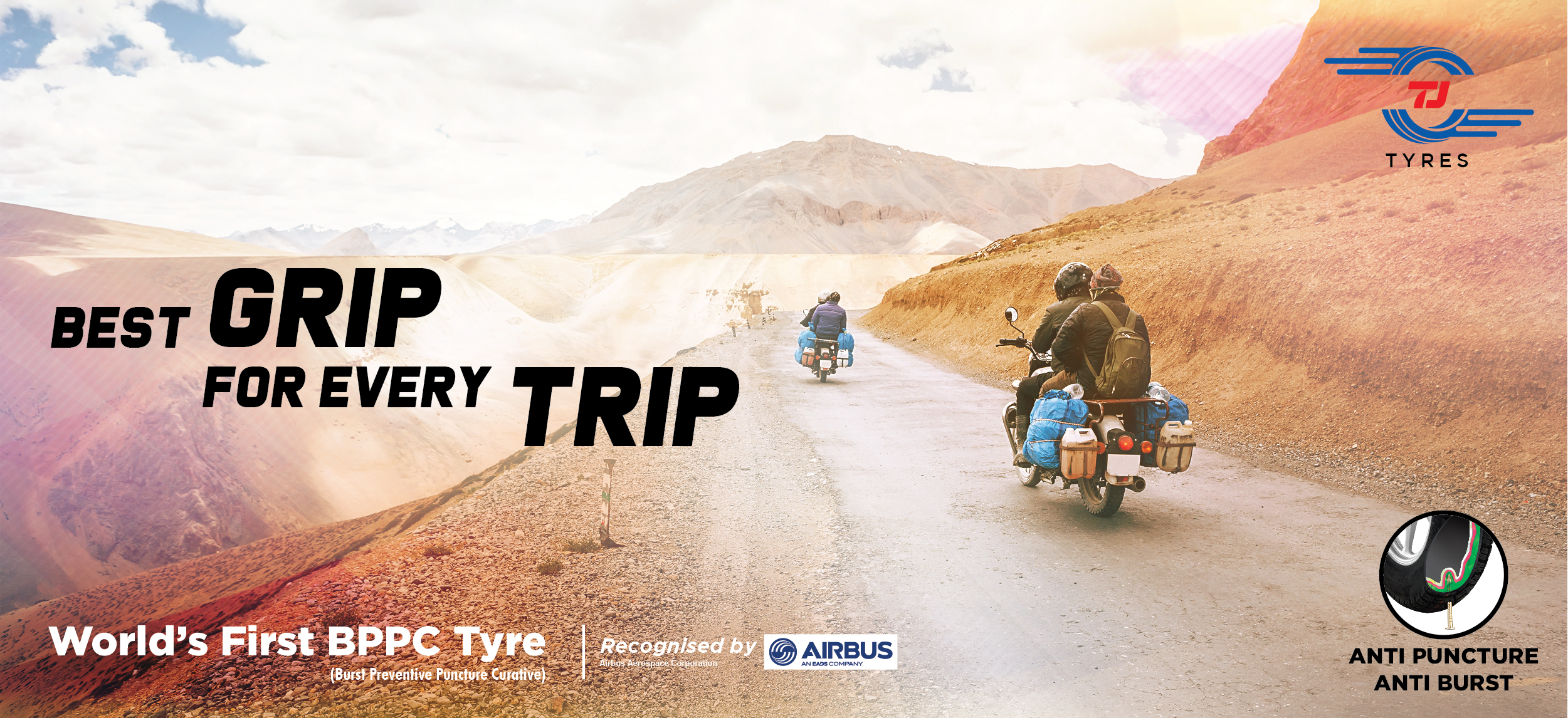
TycheeJuno (TJ) Tyres is an innovation and technology-driven start-up working on riders' and passengers' safety and fuel economy consistent with Eco-friendly solutions. TJ Tyres has the Vision to create an ecosystem on mobility & logistics focusing on innovation, safety, efficiency & decreased carbon-footprint. TycheeJuno has R&D centers in India and the USA, which are working towards developing state-of-the-art products to ensure compatibility and adaptability by our customer base in the Automobile and Allied Industries.
Our inventions are generations ahead offering normal tubeless tyres at similar tyre prices, ensuring road safety for all. Run Flat Tyres (RFT) is not available for many segments of vehicles; our technology can be adopted in all kinds of motorcycles, scooters, cars, trucks and buses. We offer an RFT at the price of tubeless tyre.
Now, seeing the COVID-19 pandemic situation and mandatory social distancing, TJ Services is bringing new innovative IT solutions for touchless transitions for all automobile-related transactions including fuel discounts. It'll prevent the spreading of the Wuhan Corona Virus to-and-through logistics partners.
If you have any questions, Please send your message
+91 129 297 9663
contact@tjtyres.com
Plot no 1, near FIT Gate, Sector 57, Faridabad, Haryana 121004
Tubeless Tyre for Bike
India’s Best Bike Tyres
India’s Best Scooty Tyres
Best Electric 2-Wheeler Tyres in India
Best Tyre Dealership in India
India’s Best BPPC Tyres